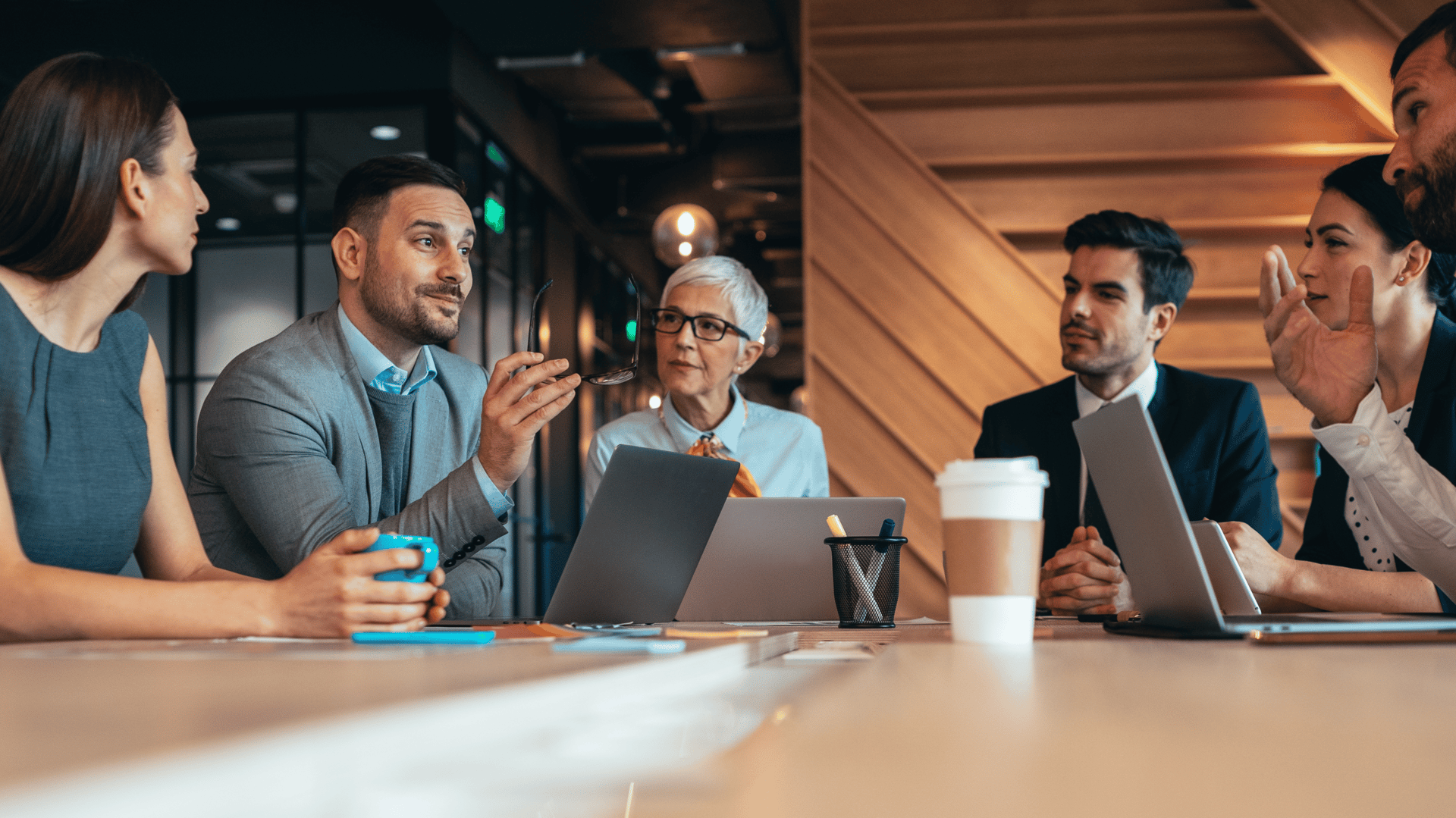
Lean Six Sigma Implementation: Elevate Your Operations to World-Class Standards
Dramatically improve quality, eliminate waste, and boost efficiency with our expert Lean Six Sigma implementation services.
Free initial consultation. Response within 24 hours.
What is Lean Six Sigma Implementation?
Lean Six Sigma is a powerful methodology that combines Lean's focus on eliminating waste with Six Sigma's emphasis on reducing variability. Our implementation service guides your organization through the adoption of these principles, resulting in streamlined processes, improved quality, and significant cost savings.
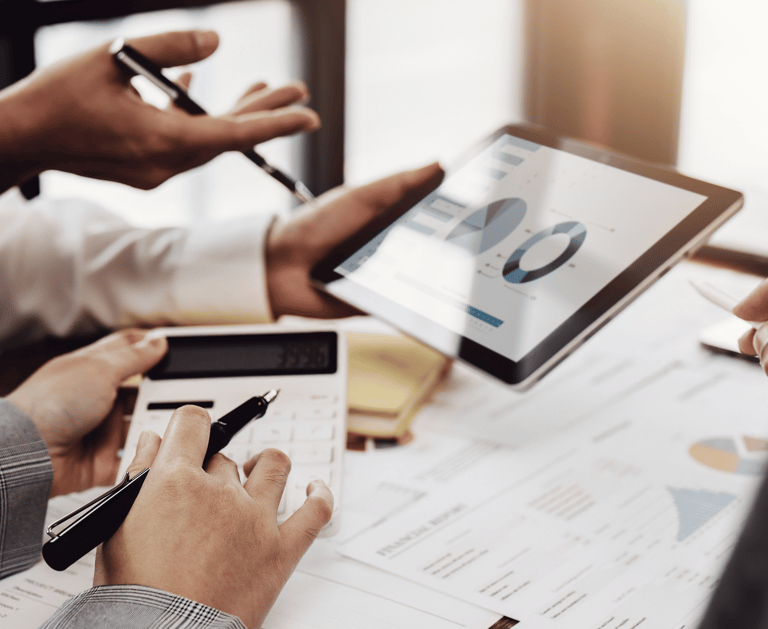
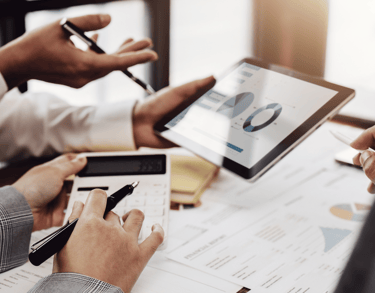
When to Implement Lean Six Sigma?
When facing quality issues or high defect rates
To reduce operational costs and improve efficiency
When seeking to enhance customer satisfaction
To standardize processes across different departments or locations
As part of a continuous improvement initiative
If you're committed to operational excellence and data-driven improvement, this service is for you.
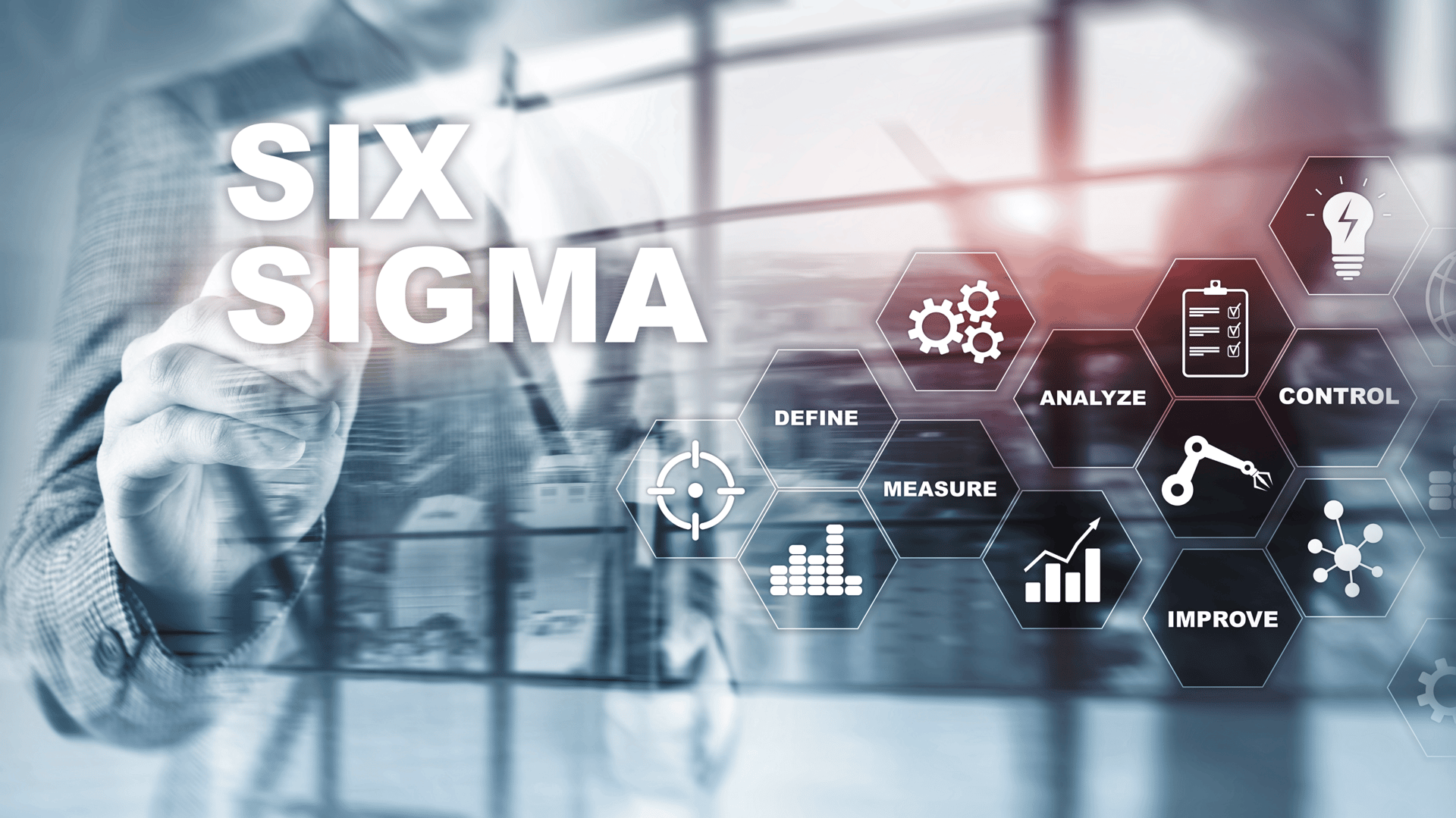
Our Lean Six Sigma Implementation Process
Assessment: Evaluate current processes and identify improvement opportunities.
Training: Educate key personnel on Lean Six Sigma principles and tools.
Project Selection: Identify high-impact projects for initial implementation.
Implementation: Guide teams through DMAIC (Define, Measure, Analyze, Improve, Control) methodology.
Sustainment: Establish systems for ongoing improvement and cultural transformation.
Key Activities
Value Stream Mapping to visualize and optimize processesStatistical
Process Control (SPC) implementationRoot
Cause Analysis using advanced tools (e.g., Fishbone diagrams, 5 Whys)
Design of Experiments (DOE) for process optimization
Kaizen events and Rapid Improvement Workshops
Benefits of Lean Six Sigma Implementation
Significantly reduce defects and process variability
Eliminate non-value-added activities and reduce waste
Improve customer satisfaction and loyalty
Enhance employee engagement through problem-solving empowerment
Create a culture of continuous improvement
Service Highlights
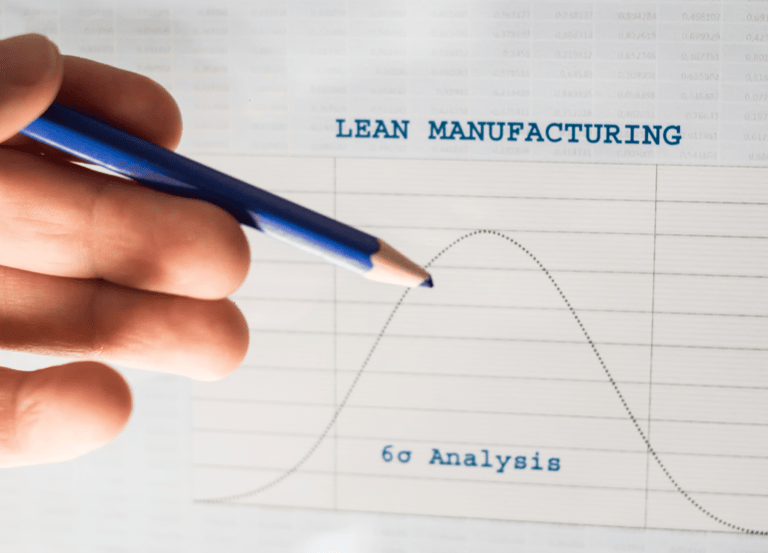
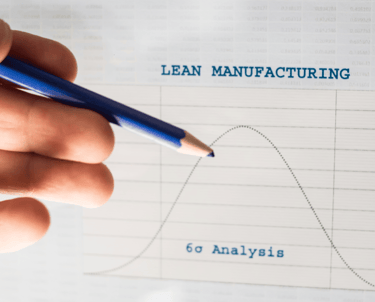
Certified Black Belt and Master Black Belt consultants leading the implementation
Comprehensive training programs for all levels (White, Yellow, Green, Black Belts)
Customized implementation plan tailored to your organization's needs
Proven track record with 95% of clients achieving or exceeding ROI targets
Tangible Impacts
25-70% reduction in process cycle times
Up to 50% decrease in defect rates
Average of 30% improvement in customer satisfaction scores
Typical ROI of 3:1 to 5:1 within the first year
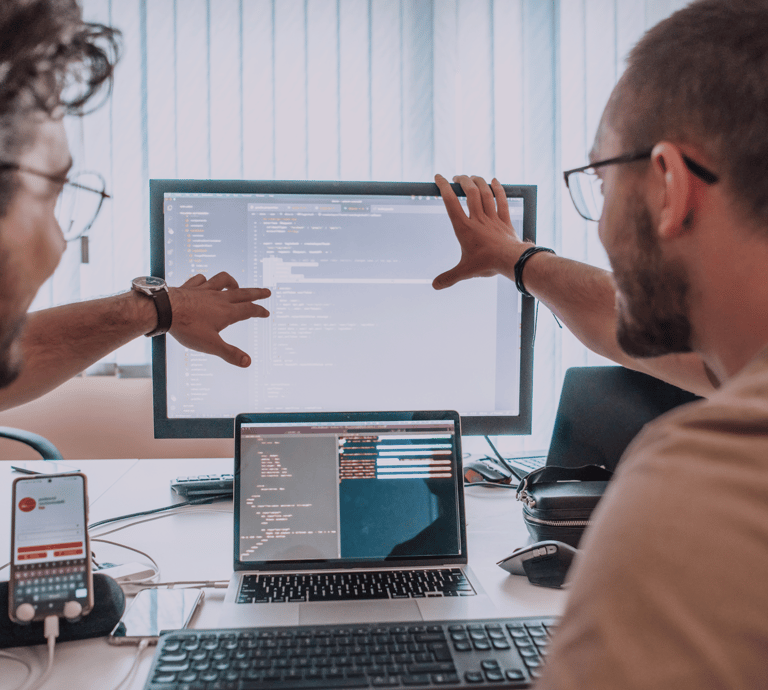
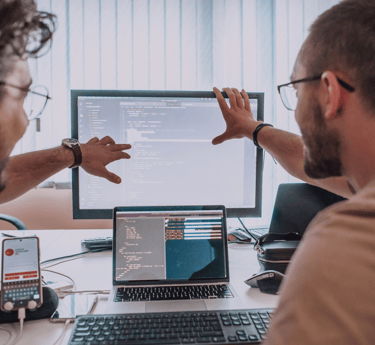
Ingenionic's Lean Six Sigma implementation transformed our manufacturing process. We've reduced defects by 60% and cut lead times in half, resulting in significant cost savings and happier customers.
CEO of Gozz Cuero Calzado
Your consultation includes a preliminary process assessment and potential improvement areas identification.
Ready to Transform Your Operations?
Frequently asked questions
How long does Lean Six Sigma implementation take?
The initial implementation typically takes 3-6 months, with ongoing projects and cultural transformation continuing beyond that.
How do you ensure the sustainability of improvements?
We focus on cultural transformation and knowledge transfer, ensuring your team can continue driving improvements long after our engagement ends.
Do we need prior Lean or Six Sigma experience?
No prior experience is necessary. Our program includes comprehensive training for all levels of your organization.
Can Lean Six Sigma be applied to service industries?
Absolutely. While originating in manufacturing, Lean Six Sigma principles are highly effective in service industries, healthcare, finance, and more.
Embark on Your Journey to Operational Excellence!
Join the ranks of world-class organizations that have revolutionized their operations through Lean Six Sigma. Your transformation starts here.
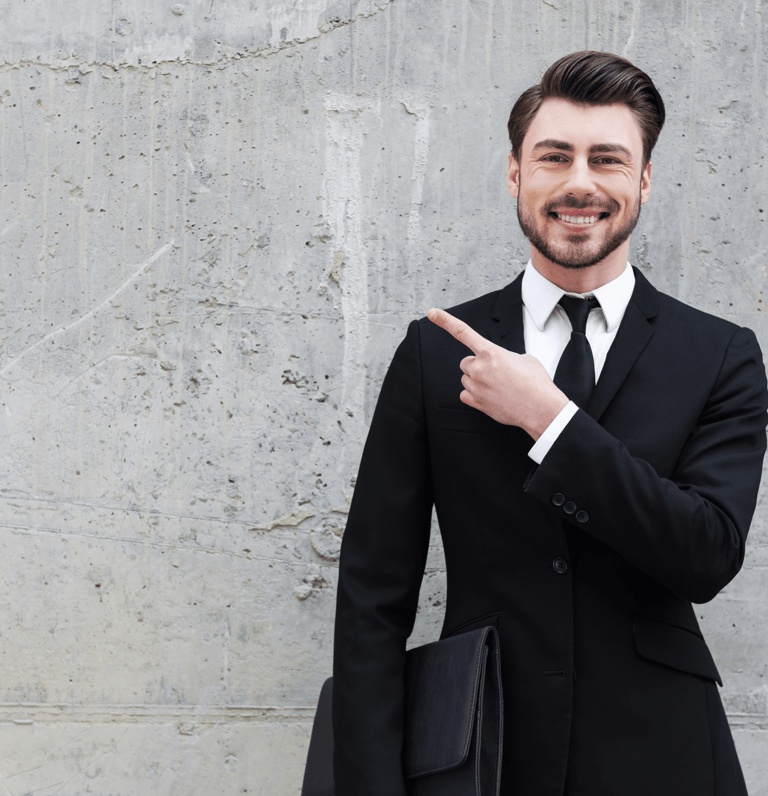
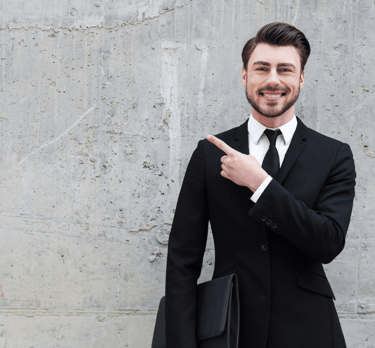
Location
Oceran Business Plaza. 19th Floor. Marbella, Panamá city, Panamá
Hours
I-V 9:00-18:00
VI - VII Closed